Why 10phase

Financial Impact: A Domino Effect on Operations
Unplanned Downtime: The Silent Profit Killer
Improper maintenance leads to unexpected equipment breakdowns, causing production delays and substantial financial losses. Industries across the board face the burden of downtime, often costing much more than anticipated. For example:
-
Manufacturing Industry: Downtime in a major automotive plant can cost up to $260,000 per hour, compounding with each hour of delay.
-
Energy Sector: In the case of power plants, a turbine failure can escalate to losses of over $1 million per day, especially during peak demand periods.
-
Transportation: Airlines facing mechanical issues can lose tens of thousands per delayed flight, not to mention the reputational cost of customer dissatisfaction.
Repair Costs: The Price of Neglect
Fixing unanticipated equipment failures often comes with premium costs. These include emergency repair services, immediate procurement of replacement parts, and potentially higher labor rates. Compared to scheduled preventive maintenance, emergency repairs can cost businesses 3 to 9 times more per incident.

Energy Inefficiency: A Costly Drain on Resources
Increased Energy Consumption
Machinery that isn’t properly maintained operates less efficiently, consuming more energy to deliver the same output.
-
Manufacturing: Improperly maintained motors, conveyor belts, or HVAC systems increase energy consumption by 15% to 30%. This is an added financial burden, especially for energy-intensive industries like steel, automotive, or electronics manufacturing.
-
Energy Production: Leaky pipelines, inefficient turbines, or aging infrastructure lead to significant wastage, inflating costs and pushing up emissions.
-
Environmental Penalties: Energy inefficiency also translates to higher emissions, exposing companies to strict regulatory penalties and sustainability challenges. For instance:
-
Industrial Plants: Inefficient equipment may lead to excess emissions, resulting in fines for non-compliance with environmental standards.
-
Power Sector: Failure to meet renewable energy or carbon reduction goals could lead to reputational damage and long-term operational costs.

Safety Risks: A Threat to Life and Reputation
Employee and Public Safety
Improperly maintained equipment often becomes a safety hazard, resulting in workplace accidents, injuries, or even fatalities.
-
Construction Sites: Malfunctioning cranes or loaders are one of the leading causes of worker injuries, with lawsuits and regulatory investigations following such incidents.
-
Transportation: Faulty brake systems in fleets or aircraft components lead to life-threatening accidents. For instance, mechanical issues account for 12% of all airline accidents worldwide.
Long-Term Reputational Damage
Accidents caused by equipment failures not only bring legal consequences but also tarnish a company’s reputation. Public perception of unsafe practices can reduce customer trust, impacting sales and future growth.
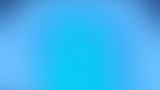
The Future with 10Phase: A Tokenized, Human-Free Asset Maintenance System
10Phase is transforming asset maintenance across industries with a robust, tokenized system powered by AI, IIoT, and blockchain. Our 10-Phase Framework ensures that your assets are always in peak operating condition, eliminating inefficiencies and delivering measurable outcomes.
Key Benefits of 10Phase Solutions
-
Cost Savings: Prevent breakdowns before they happen with predictive maintenance powered by AI.
-
Energy Efficiency: Optimize energy usage with real-time monitoring and automated adjustments.
-
Safety and Compliance: Achieve a safer work environment with consistent monitoring and proactive interventions.
-
Sustainability: Reduce waste and emissions with IIoT-enabled asset tracking and rule-based management.